
The core principle of high-efficiency dehumidification
In-depth understanding of the working mechanism of refrigerated compressed air dryers, especially the process of removing excess water using low-temperature condensation technology. This equipment liquefies the water vapor into a liquid by cooling the air to its dew point temperature and is separated. The treated air becomes dry and clean, meeting the demand for high quality anhydrous gas in industrial production and laboratory environments.
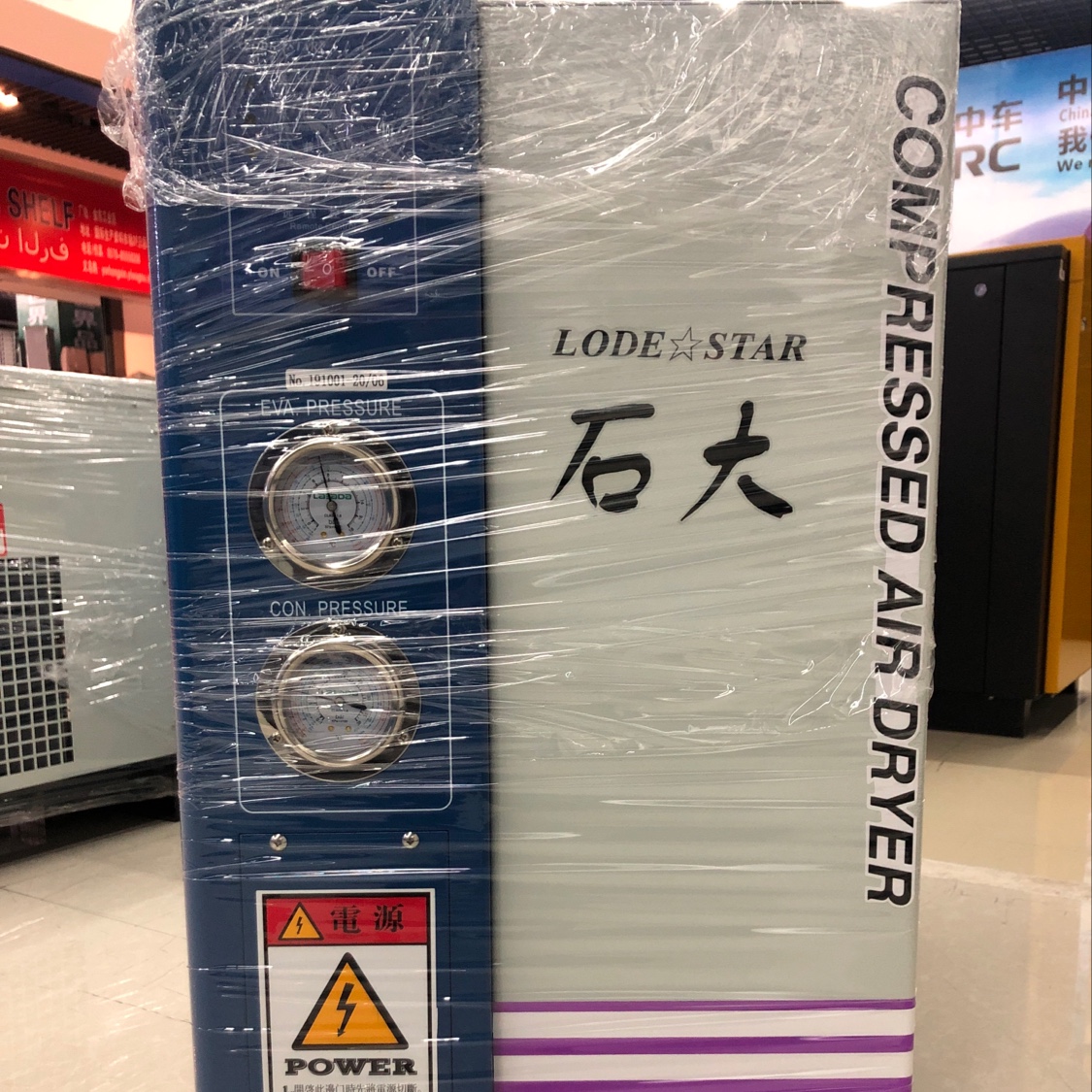
This process can not only effectively remove moisture from the air, but also filter out other impurities and particles, ensuring that the final gas is clean and dry. This is essential for businesses that rely on high-quality compressed air for their operations.
The key to improving work efficiency
With the introduction of refrigerated compressed air dryers, companies and research institutes can significantly reduce downtime and maintenance frequency. Traditionally, the existence of humidity may cause problems such as rust of mechanical equipment and moisture of electronic components. These problems will directly affect the continuity of production and product quality. However, when refrigerated compressed air dryers are used, these problems will no longer exist.
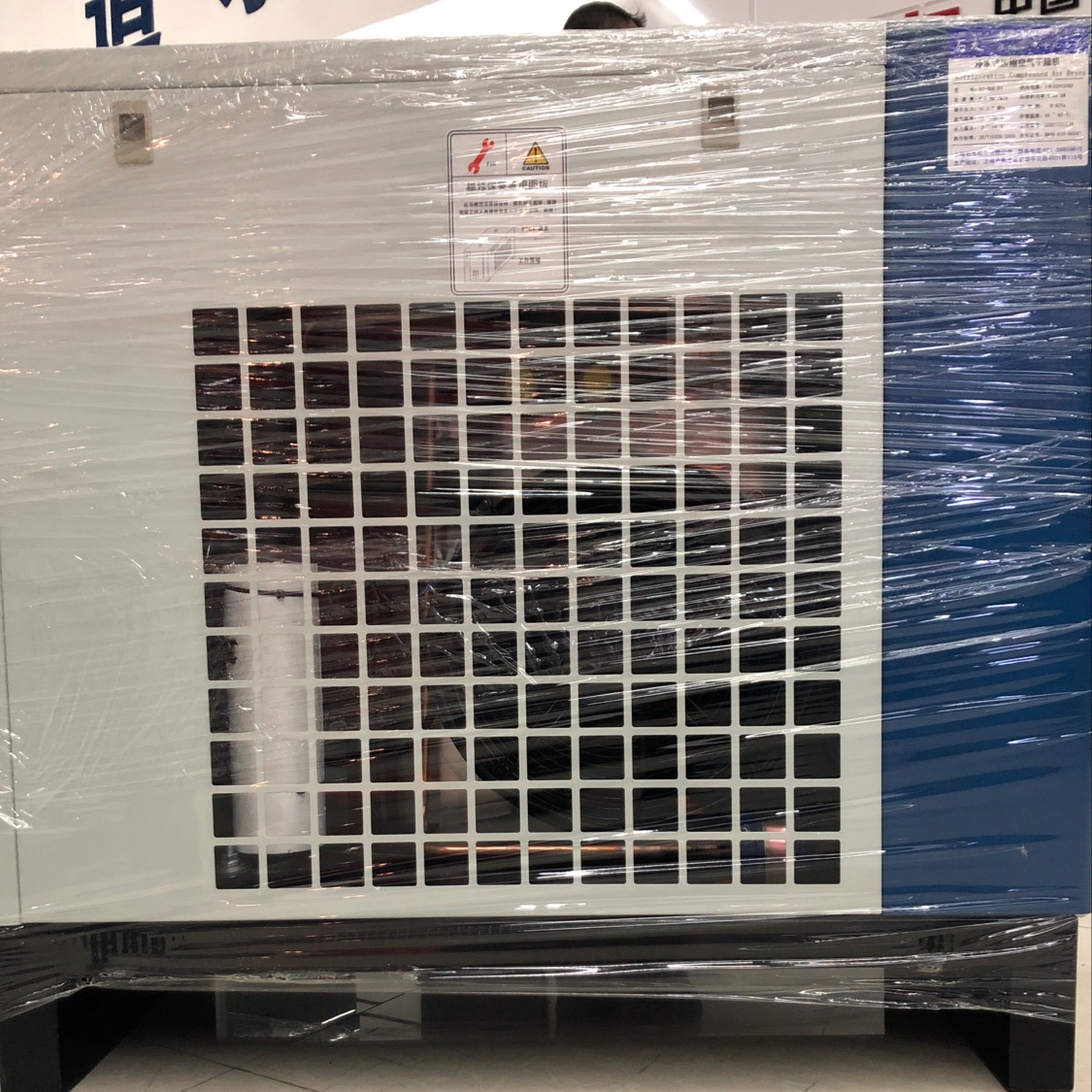
The continuous supply of a stable and clean gas source means that the production line can run more smoothly and the experimental operation is no longer affected by the external environment. As a result, the productivity of the entire enterprise has been greatly improved, and quality control has become easier to achieve high standards.
Effective ways to reduce maintenance costs
After the humidity problem is solved, the corrosion rate of related mechanical parts is significantly slowed down, and the replacement cycle of parts can be extended, thereby reducing the overall operating cost. Specific case studies have shown that some critical components may cause frequent failures or even early scrap due to moisture before appropriate measures are taken. However, since the use of high-performance refrigerated compressed air dryers, this situation has undergone a fundamental change.
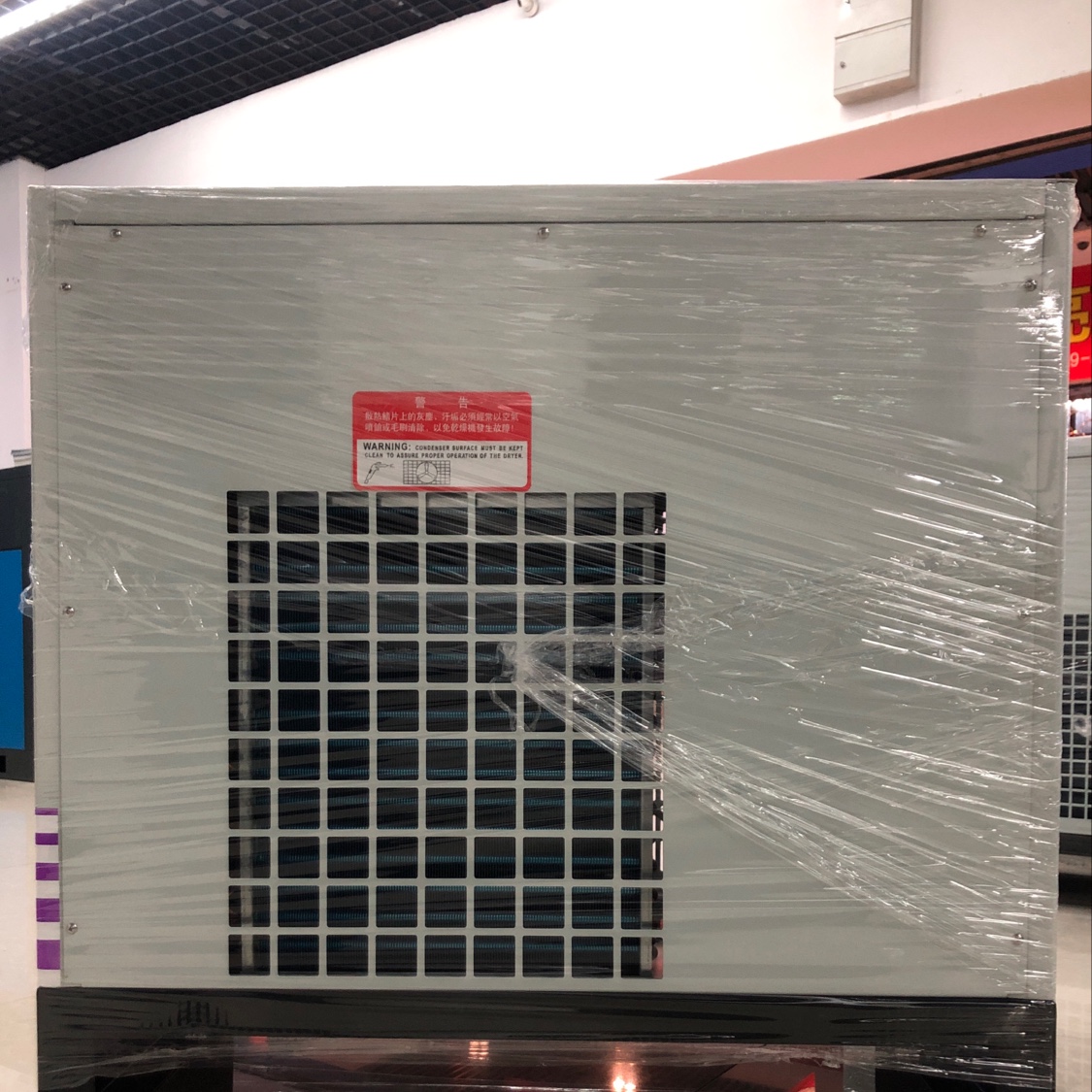
In the long run, this investment not only helps companies save a lot of maintenance funds, but also indirectly promotes the overall life of the equipment, bringing higher economic and social benefits.
Ability to respond to complex environmental challenges
Whether in high temperature and high humidity areas or extreme cold weather conditions, refrigerated compressed air dryers can perform well. Especially in some special industries, such as food processing and pharmaceutical fields, air quality standards are very high. This kind of equipment just meets their requirements, because it can maintain good performance in various harsh environments, and there will be no functional failure caused by excessive temperature difference.
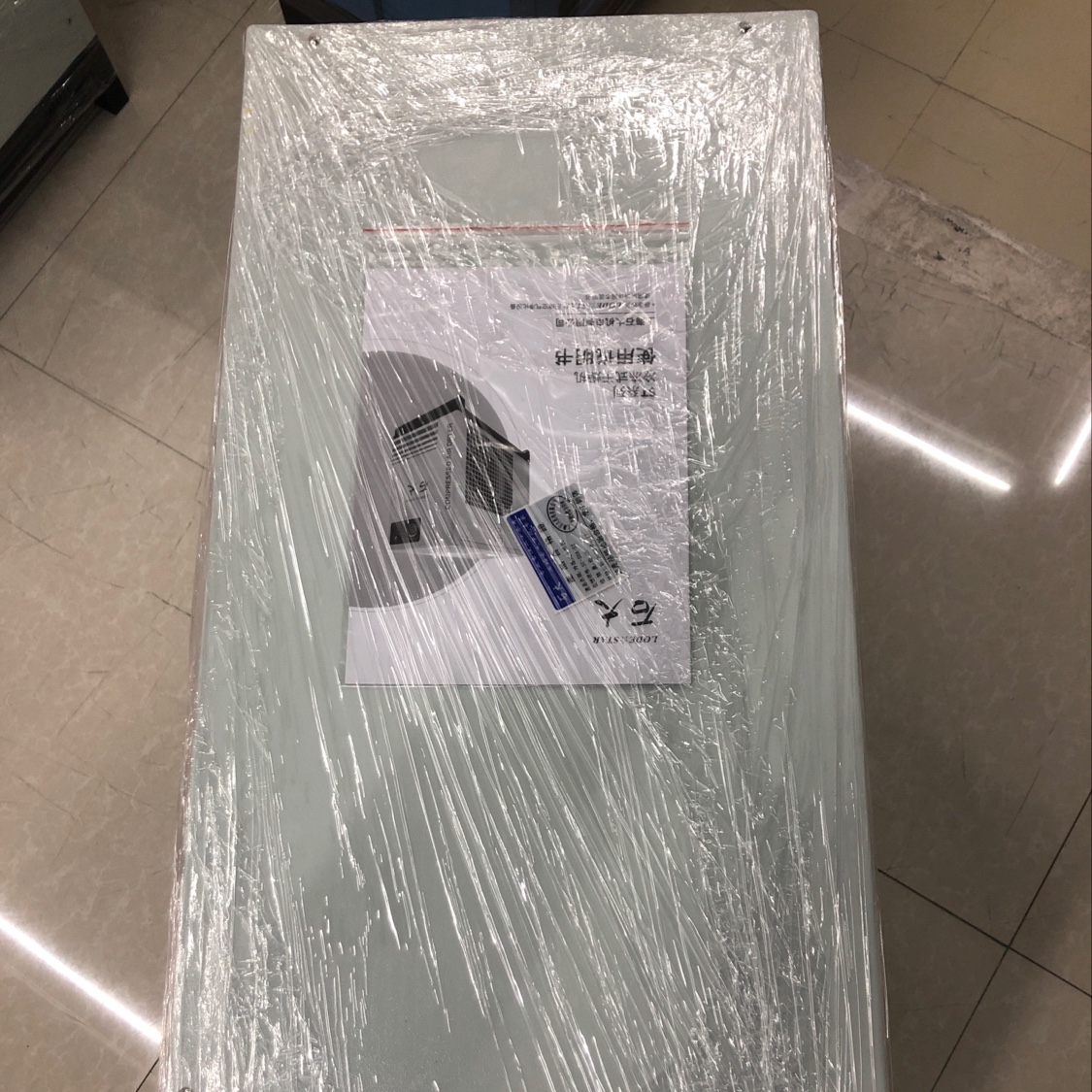
With excellent design and technical support, refrigerated compressed air dryer has become one of the best choices for many enterprises in the face of different working conditions.
Solutions for Diversified Application Scenarios
From manufacturing to healthcare to scientific research and other fields, refrigerated compressed air dryers are favored for their wide applicability. Different industries have different needs, but each customer can find a product configuration solution that suits their own situation. Here are some examples:
a large automobile manufacturer: has realized zero pollution emission on automatic spraying line;
well-known pharmaceutical enterprise research and development center: to ensure the absolute purification conditions required in the pharmaceutical production process;
top university laboratory: provides the most reliable protective barrier for precision instruments.
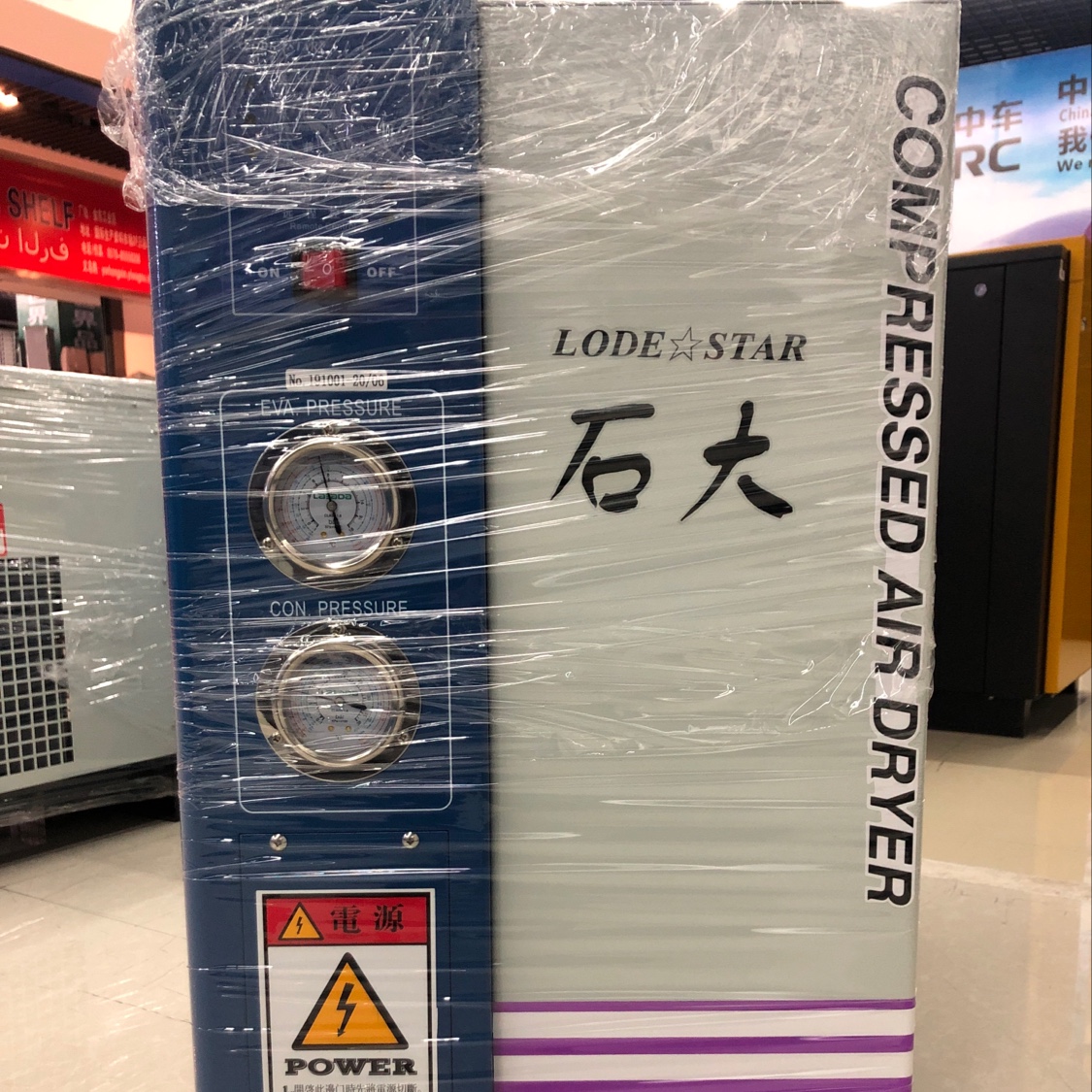
The above case shows the strong adaptability and great value of the refrigerated compressed air dryer.
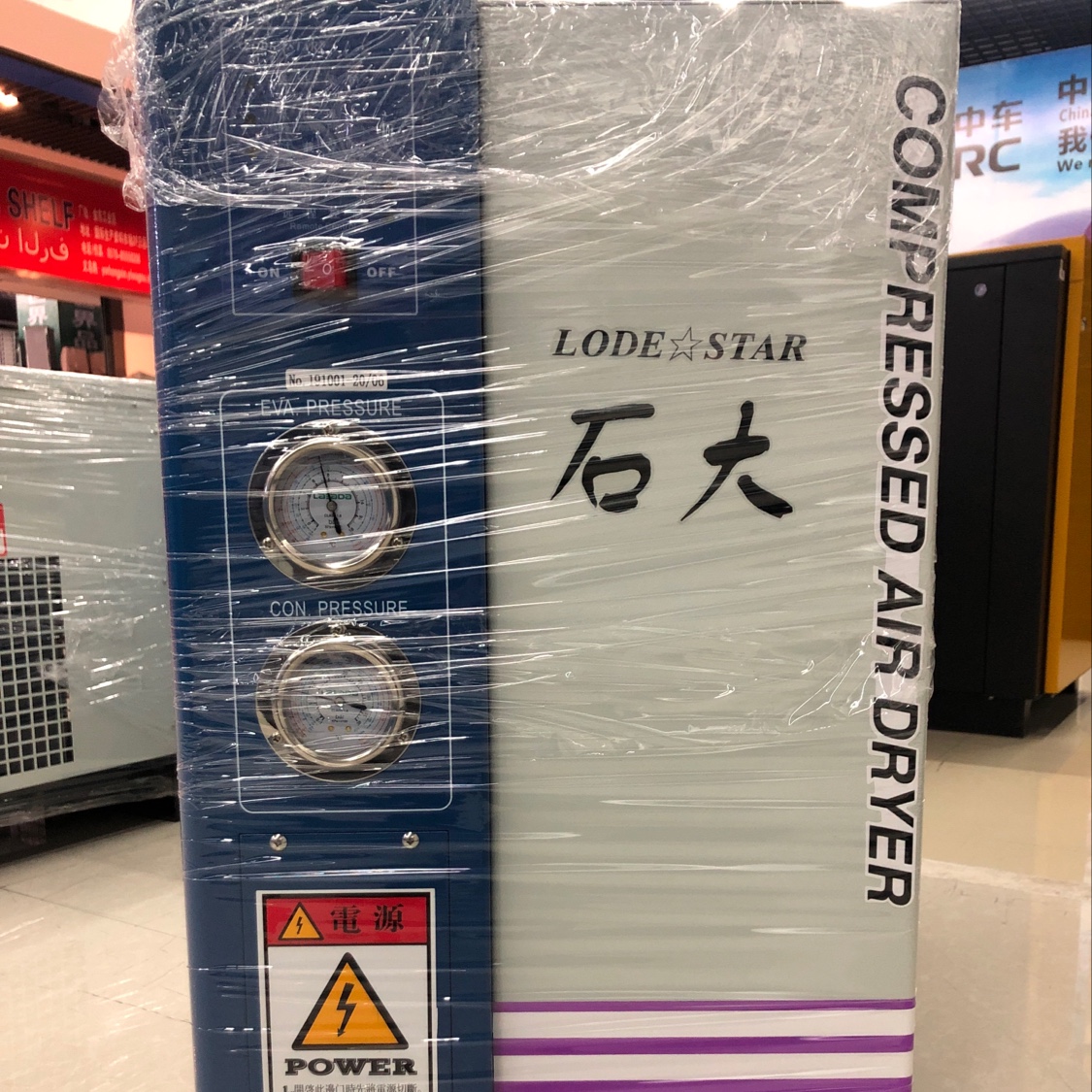