
What is a refrigerated compressed air dryer
Refrigerated compressed air dryer is a device that uses refrigeration technology to remove moisture from compressed air. It reduces the temperature of the air to condense the water vapor into liquid, thereby achieving efficient dehumidification. Such equipment plays a vital role in industrial production, especially in environments that require a high degree of cleanliness and stability. This section provides an in-depth analysis of the basic concepts and operating principles of refrigerated compressed air dryers.
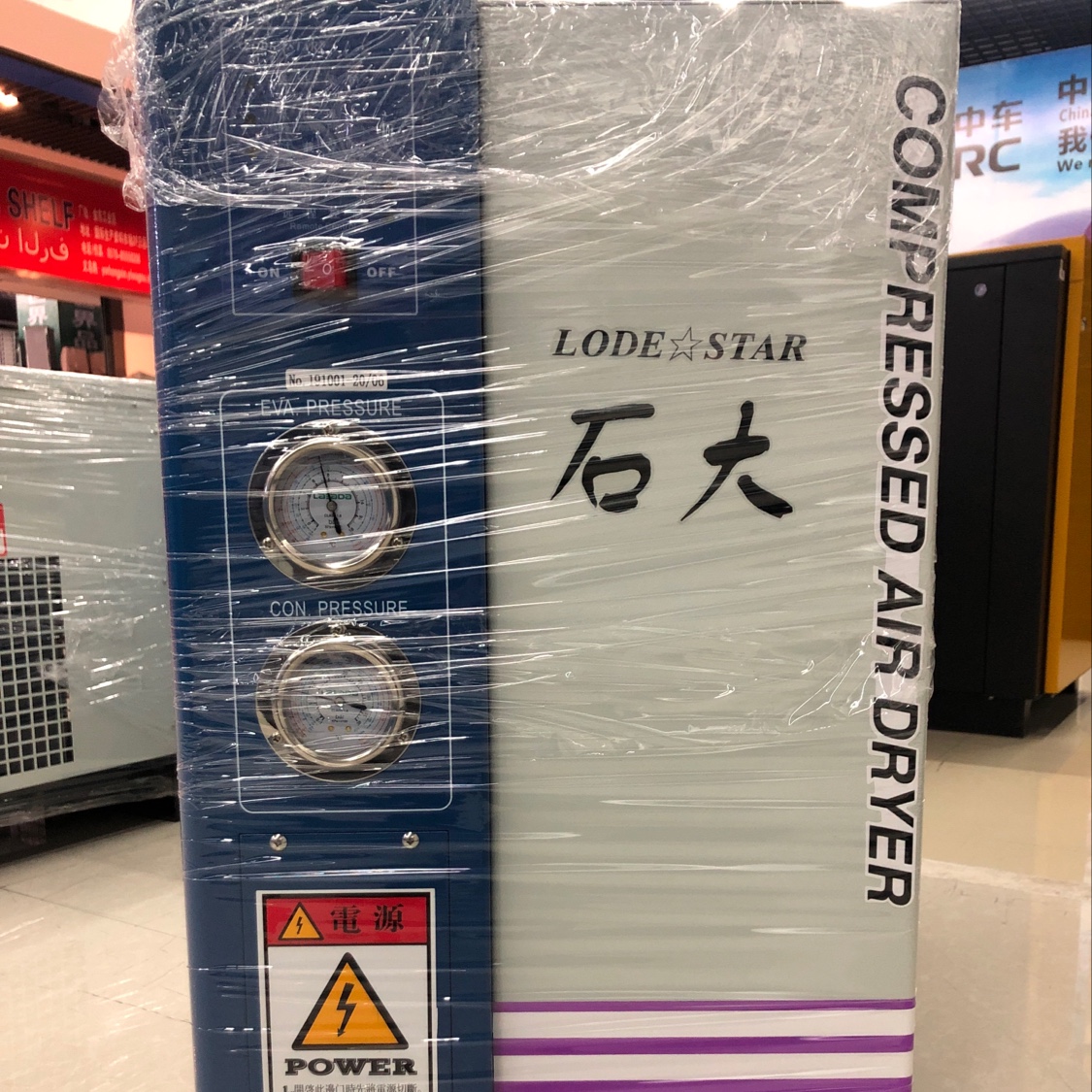
Core components of refrigerated compressed air dryer
Understanding the core components of refrigerated compressed air dryers is essential for selecting and maintaining equipment. The equipment mainly includes key components such as refrigeration system, heat exchanger, filter and control system. The refrigeration system is responsible for cooling the compressed air to reach the dew point temperature, so that the water vapor is condensed into liquid; the heat exchanger is used for heat transfer and recovery; the filter can further purify the compressed air and remove impurities; the control system ensures the equipment Normal operation and parameter adjustment. Each component has its own unique role, together constitute an efficient and reliable dehumidification system.
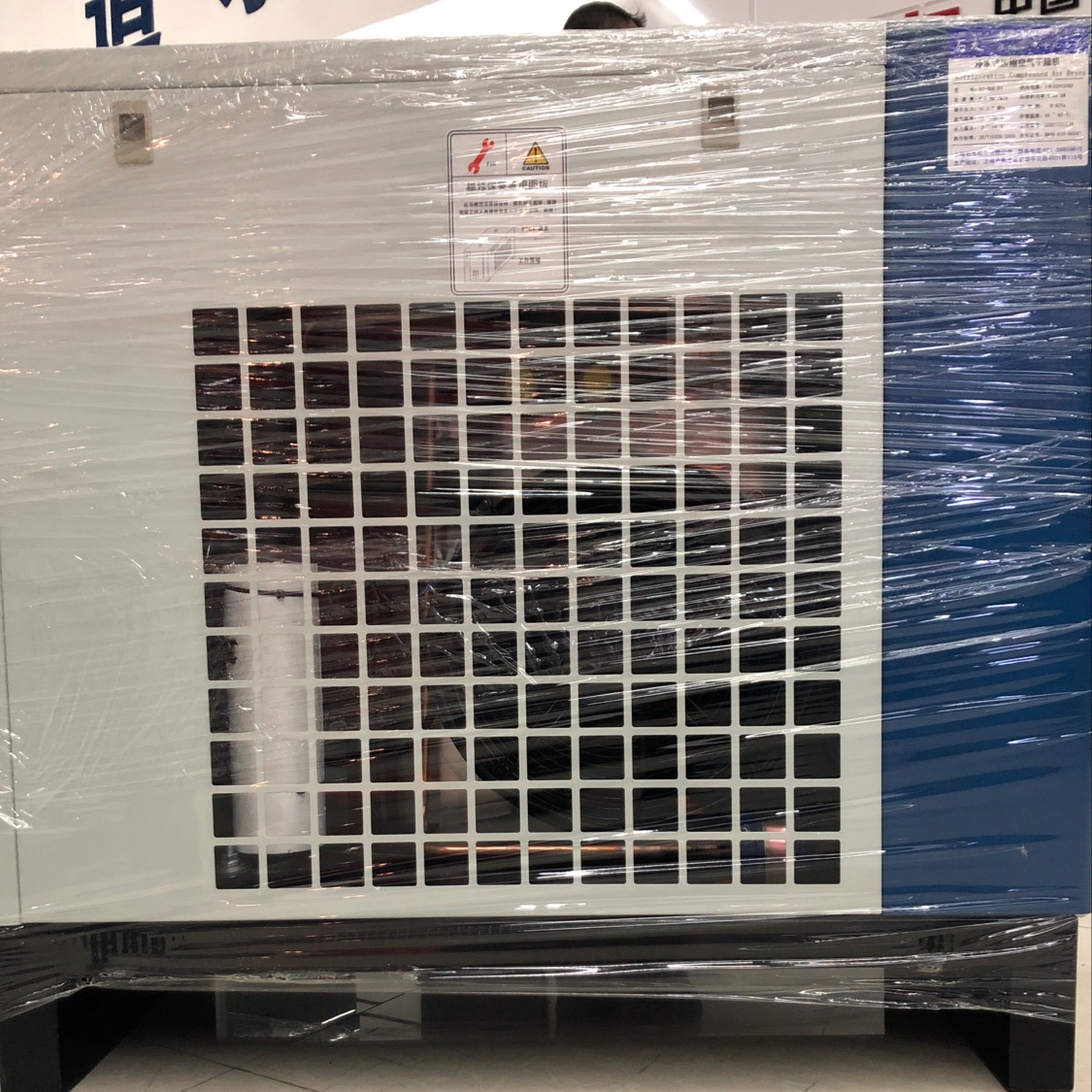
Application Scenarios of Refrigerated Compressed Air Dryer
Refrigerated compressed air dryers are widely used in many industrial fields, including food processing, pharmaceuticals, and electronic manufacturing. In the food processing industry, it can ensure the air quality on the production line and prevent corruption and pollution caused by moisture; in the pharmaceutical field, it can maintain a clean environment in the pharmaceutical production and packaging process and ensure product quality; in the electronics manufacturing industry, It can prevent the influence of humidity on precision components and improve the yield of products. We will analyze the specific application cases in these fields one by one, and show the important role of refrigerated compressed air dryer in actual production.
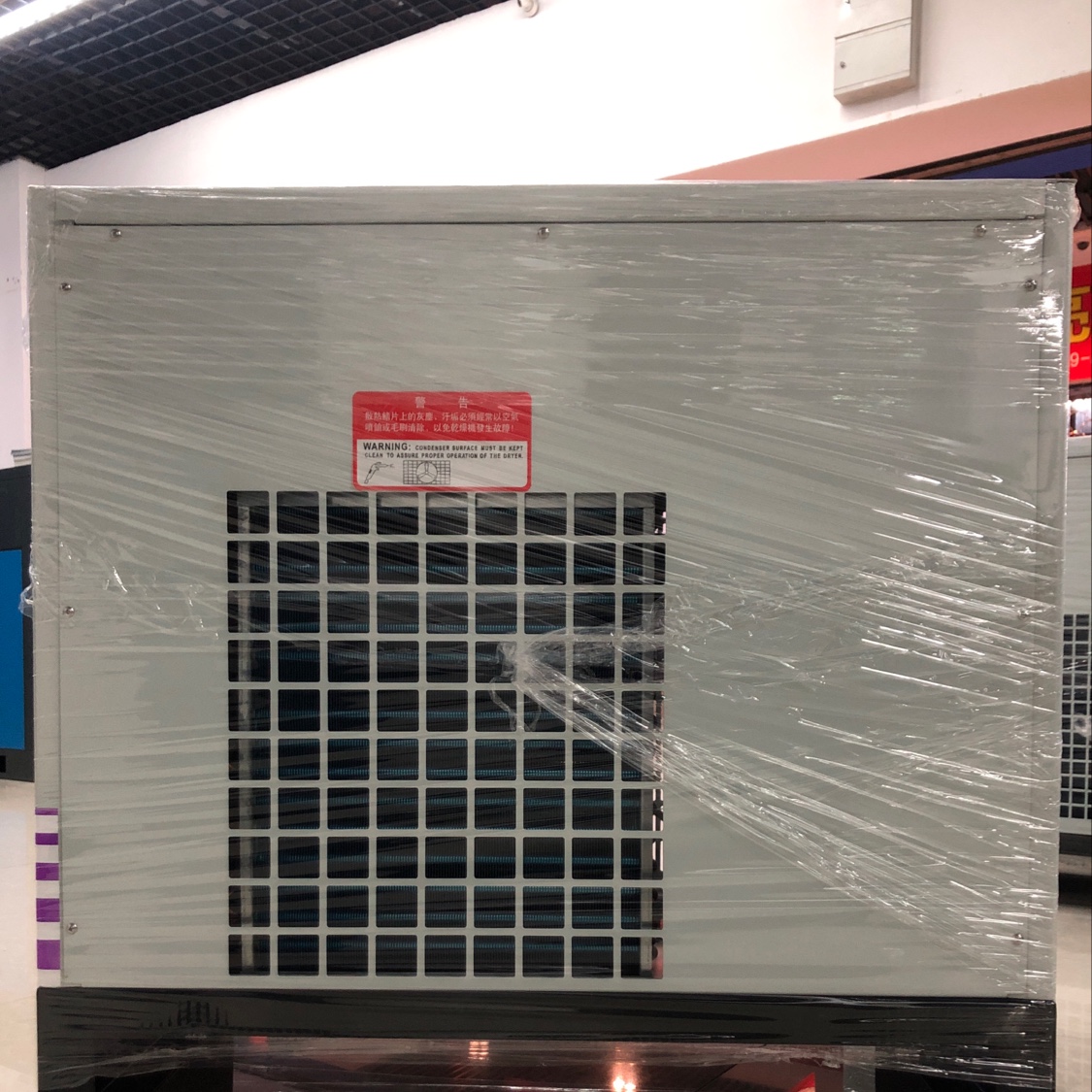
Five criteria for choosing a refrigerated compressed air dryer
There are many brands of refrigerated compressed air dryers on the market. How to choose the most suitable equipment for you? The following are the five criteria for choosing refrigerated compressed air dryers:
1. Dehumidification capacity: Different production environments have different requirements for dehumidification capacity. The maximum processing capacity and dew point temperature of the equipment should be considered when selecting to ensure that the actual demand is met.
2. Energy efficiency: Efficient energy use can not only reduce operating costs, but also reduce carbon emissions and protect the environment. Choosing energy-efficient equipment is a wise choice.
3. Reliability: The stability and durability of the equipment directly affect the continuity and safety of production. Choosing well-known brands and certified products can increase reliability.
4. Maintenance cost: Maintenance cost is a part of the equipment life cycle that cannot be ignored. Choosing equipment that is easy to maintain and repair can reduce long-term costs.
5. Price: Reasonable cost performance is an important factor in choosing equipment. Consider the above points to find the best balance between performance and price.
Advantages and Disadvantages of Refrigerated Compressed Air Dryers
Understanding the advantages and disadvantages of refrigerated compressed air dryers can help you make more informed decisions. The main advantages of refrigerated compressed air dryers are their efficient and stable dehumidification capacity and low initial investment costs. However, its energy efficiency is relatively low and it may not perform well in extremely low temperatures. In contrast, although the initial investment is higher, the adsorption dryer is more energy efficient and suitable for lower dew point requirements. We will comprehensively compare these two types of dryers to help you weigh the pros and cons and choose the most suitable equipment for you.
Routine maintenance of refrigerated compressed air dryer
Correct maintenance and maintenance can significantly extend the service life of refrigerated compressed air dryers. Here are some practical maintenance tips:
1. Check the refrigerant level regularly: Ensure that the refrigerant is sufficient to avoid equipment failure due to insufficient refrigerant.
2. Clean the filter: Clean or replace the filter regularly to prevent dust and impurities from clogging and affecting equipment performance.
3. Check the electrical connection: Check the power cord and connector regularly to ensure that there is no looseness or damage.
4. Monitor operating parameters: Regularly record the operating data of the equipment, find abnormal situations in time and make adjustments.
Installation and commissioning of refrigerated compressed air dryer
If you plan to install a refrigerated compressed air dryer, this section will provide you with detailed installation and commissioning guidelines. From pre-preparation to final commissioning, each step will be illustrated to ensure that you can install it smoothly and use it correctly.
1. Preliminary preparation: Choose a suitable location to ensure good ventilation and keep away from high temperature and humid environment. Prepare necessary tools and materials, such as wrenches, screwdrivers, sealants, etc.
2. Installation steps: Follow the instructions in the instructions to install the refrigeration system, heat exchanger, filter and control system in turn. Ensure all components are tightly connected and leak-free
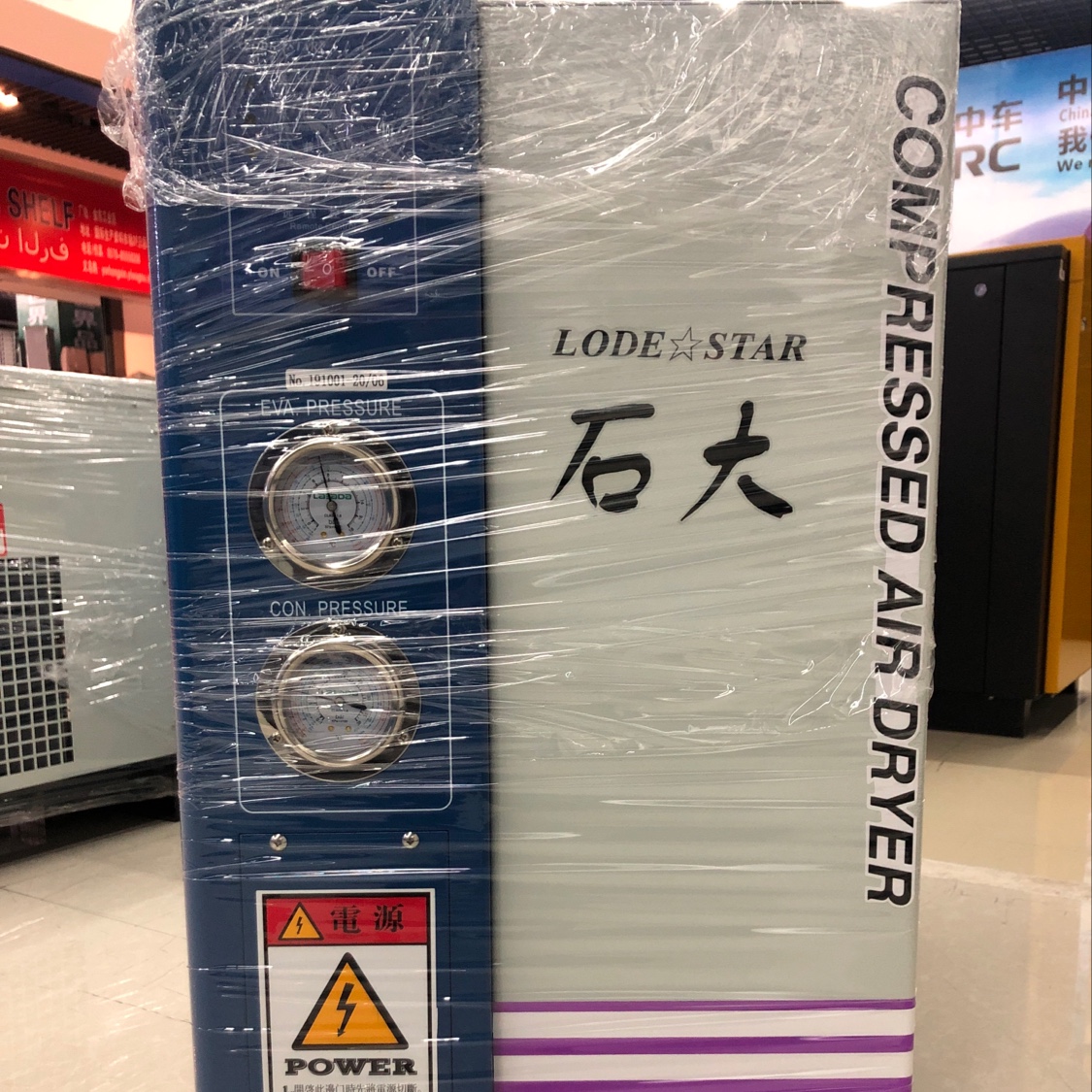