
Advanced cooling technology, excellent dehumidification capacity
The refrigerated compressed air dryer adopts leading refrigeration technology, which can effectively remove moisture and other impurities entrained in the compressed air under low temperature conditions. This process not only makes the gas more pure, but also prevents corrosion and icing inside the pipeline, ensuring stable and reliable operation of the system.
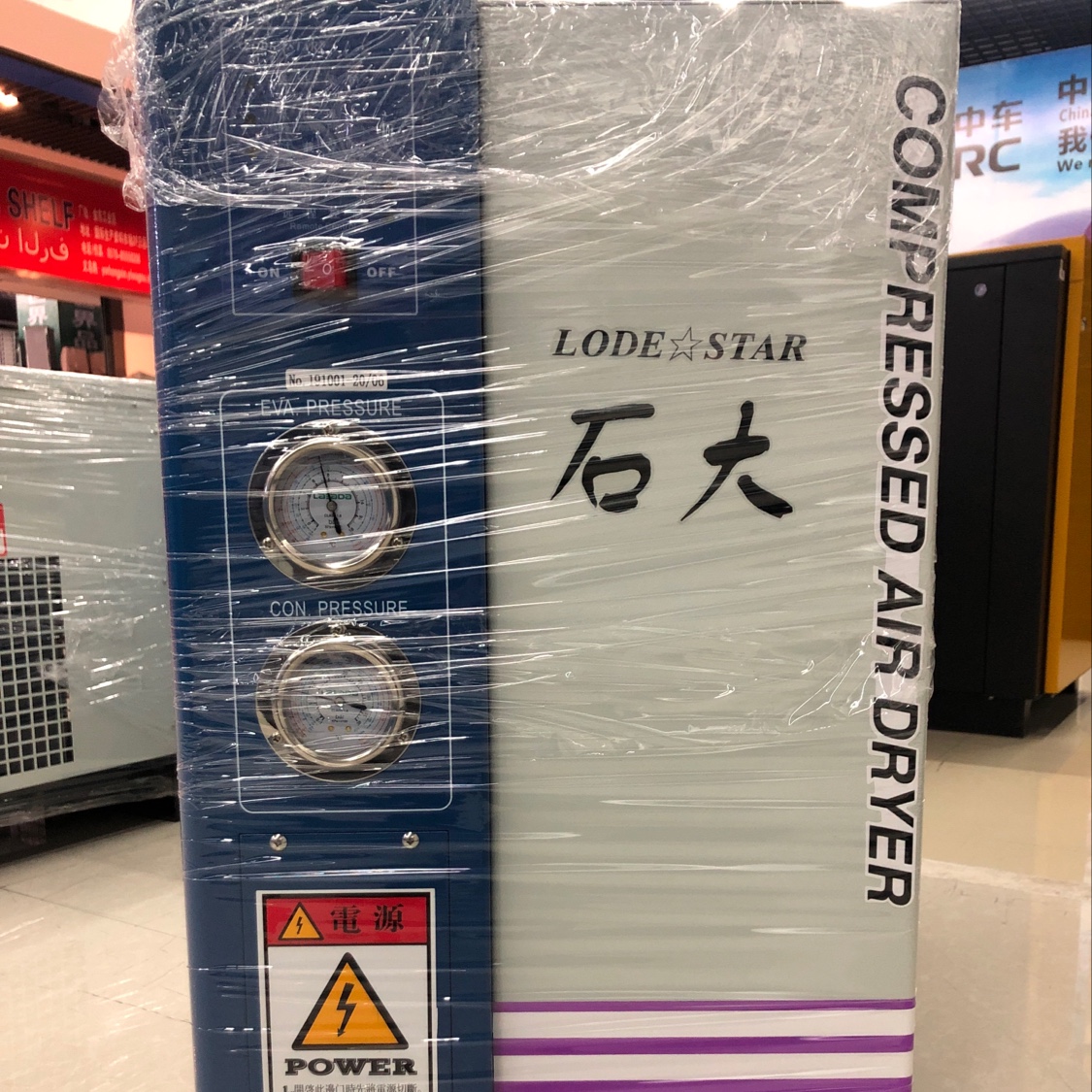
By accurately controlling the dew point value within the temperature range, refrigerated compressed air dryers can achieve the desired dehumidification effect, thereby providing high quality and stable dry air quality for use in industrial production processes in various fields.
Widely used in various industries
From precision electronics manufacturing workshops to strict food safety production lines, to chemical production environments, this type of dryer has won the favor of many companies with its excellent performance. It is an ideal choice whether in the pharmaceutical industry where humidity control is extremely demanding, or for large plants that require long-term stable gas supply.
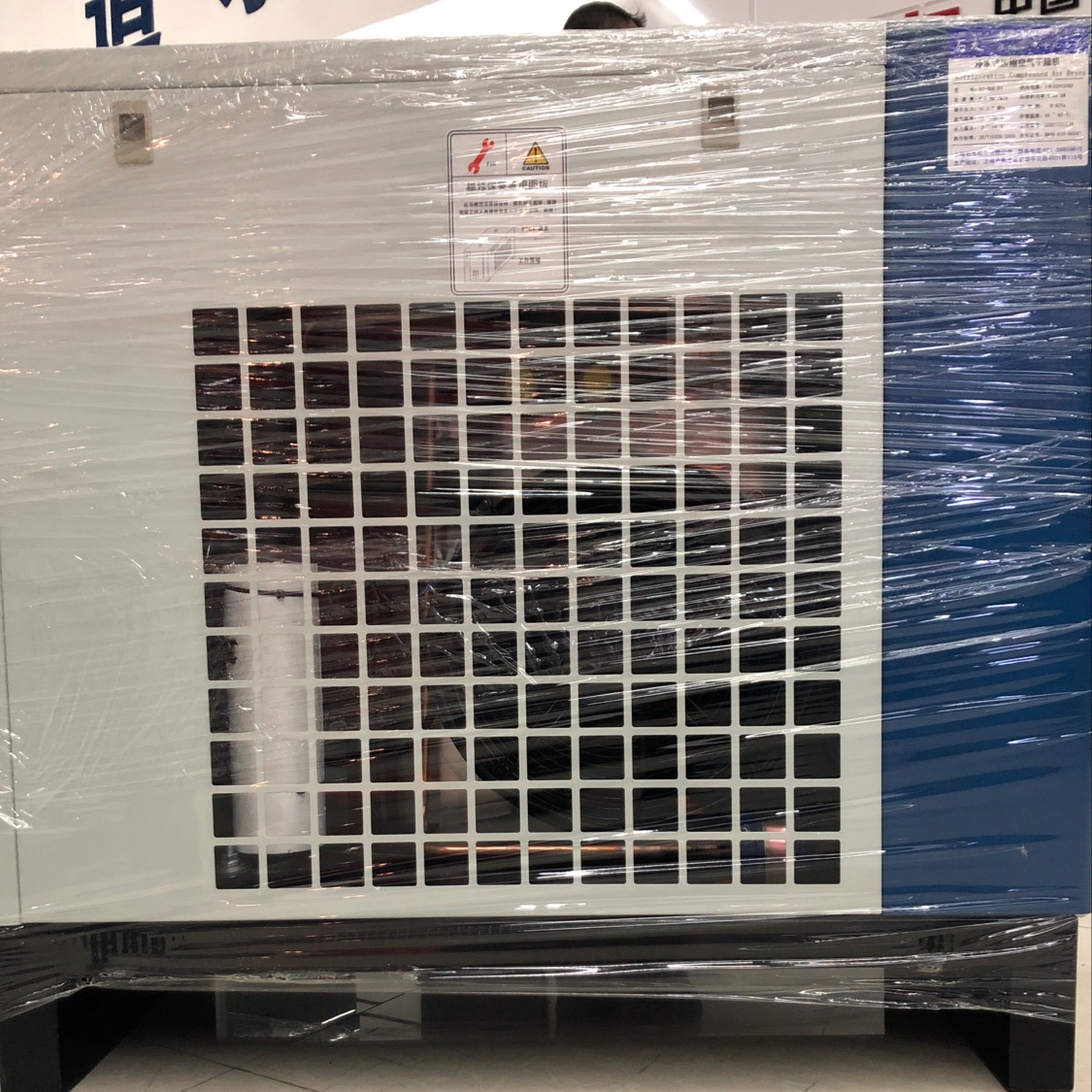
Refrigerated compressed air dryers can not only bring efficient air purification management methods for enterprises, but also greatly improve the efficiency of the production line and product quality stability, thereby promoting enterprises to occupy a favorable position in the fierce market competition environment.
Analysis of key components-the role of condenser and evaporator
As one of the core components, the condenser is responsible for converting high-temperature and high-pressure steam into liquid water and discharging it; while the evaporator reduces the temperature to promote the condensation of the remaining water vapor into liquid form to be removed. The two work together to achieve an efficient dehumidification effect and maintain the energy-saving operation of the entire system.
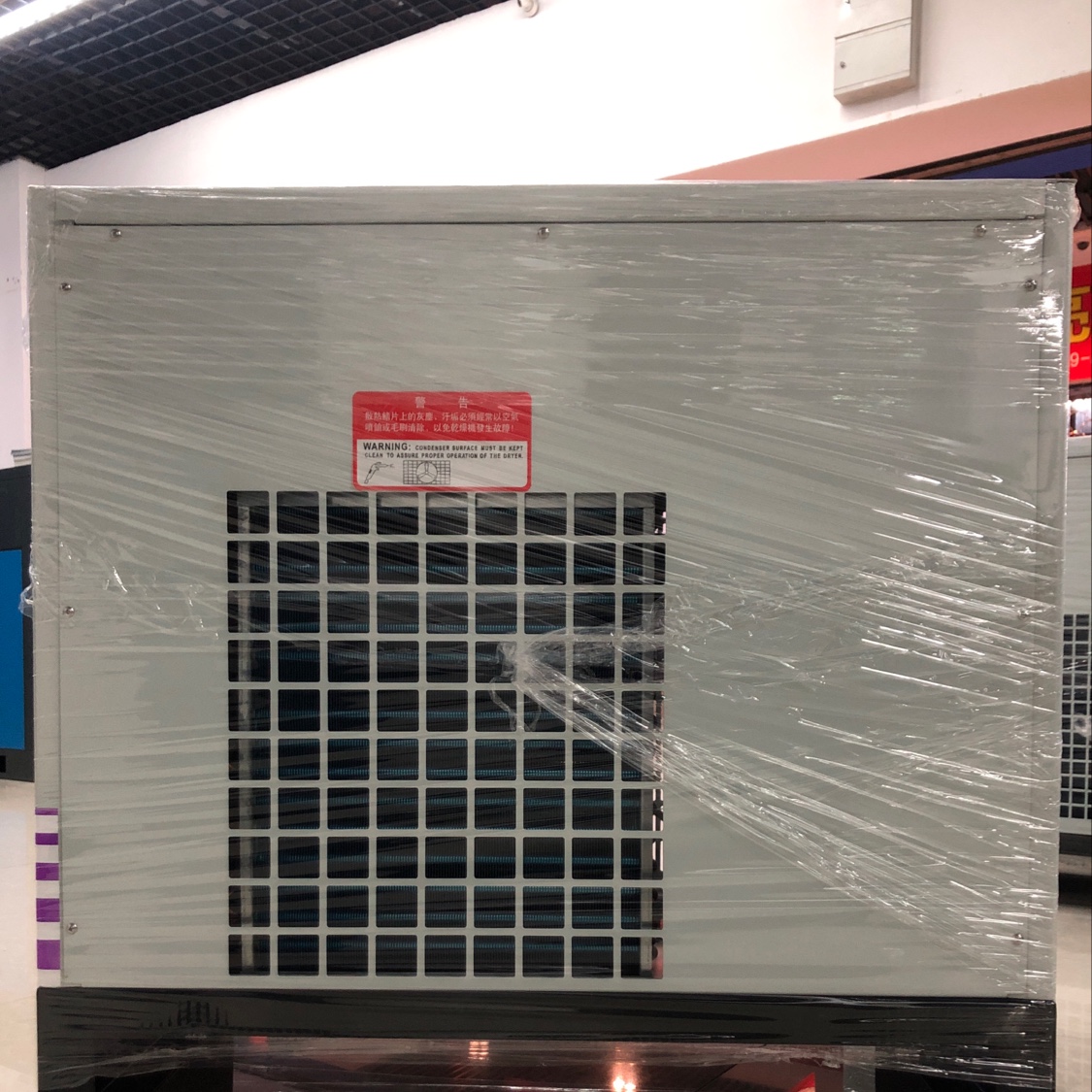
In addition to the basic functions, modern refrigerated compressed air dryers are also equipped with an intelligent control system, which can automatically adjust the degree of coordination between the two main components according to the actual situation to further optimize the overall work efficiency and energy consumption ratio.
Save costs and extend equipment life
Regular maintenance and proper use of refrigerated compressed air dryers can help companies reduce maintenance costs due to moisture and significantly improve the overall efficiency and reliability of production equipment. More importantly, it can also prevent damage to key components due to moisture, thereby significantly delaying the depreciation of assets.
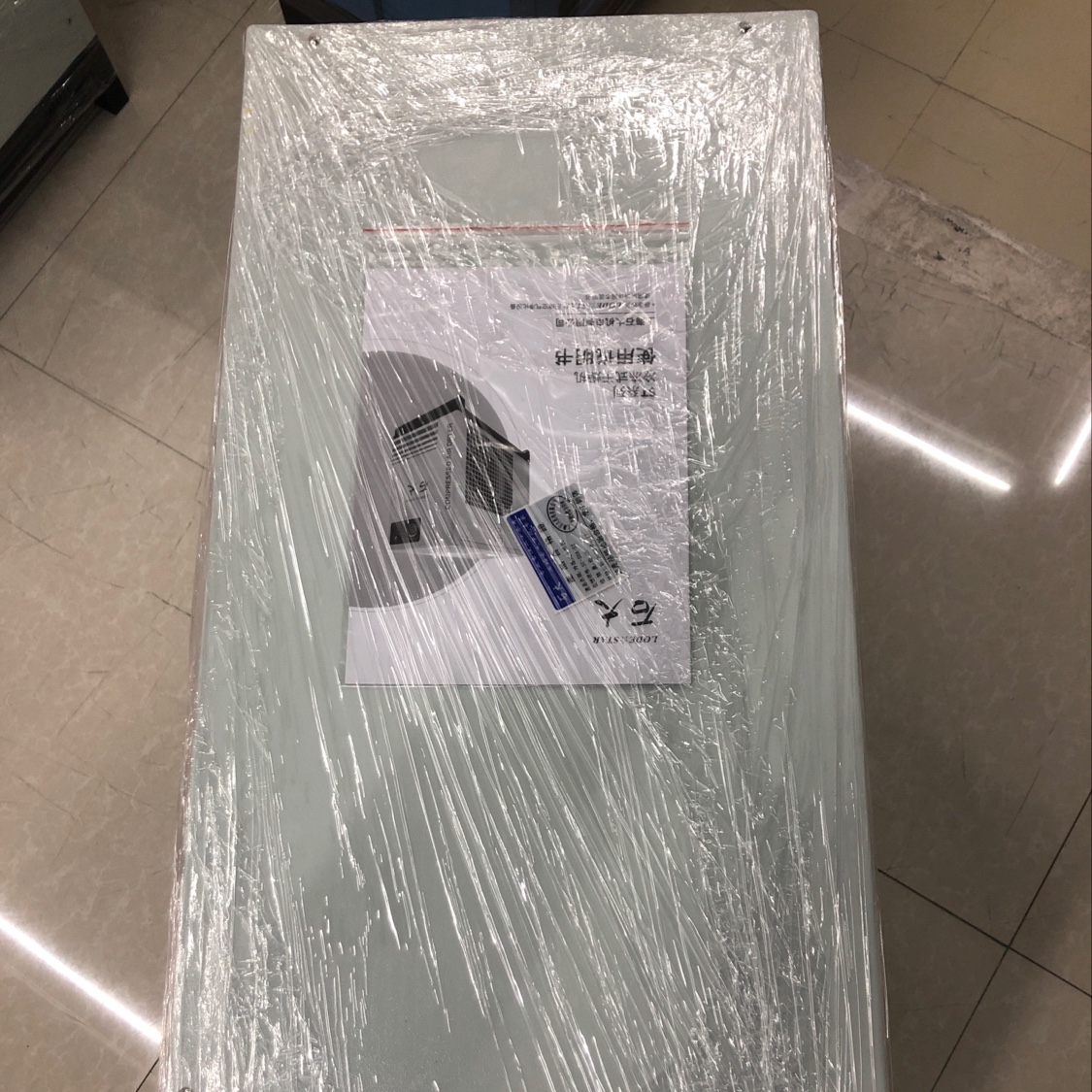
By maintaining good operating habits and timely updating and replacing consumables and accessories, users can maximize the advantages of refrigerated compressed air dryers and create greater economic benefits and social value for them.
Selection Guide: How to choose the right model and specification?
There are many types of refrigerated compressed air dryers available on the market, but not all are suitable for every specific application. Therefore, before deciding to purchase, it is important to make an informed decision after a thorough evaluation of factors such as actual operating conditions (e. g., flow size, pressure level) and budget constraints. In addition, brand reputation and service quality are also important considerations that cannot be ignored.
After understanding the special functions and technical indicators you need, combined with the supplier's technical support service level, it is the most rational way to finally select the refrigerated compressed air dryer that is most suitable for the current project.
Key points and precautions for installation and debugging
The correct installation location and method are very important, they directly affect the normal performance of the machine. In general, the instructions provided by the manufacturer should be followed to set the operation steps, including but not limited to power connection confirmation, air inlet and outlet direction adjustment, etc. At the same time, it is also necessary to pay attention to whether there is enough heat dissipation space around to ensure good ventilation.
In order to avoid unnecessary troubles and obtain a better performance experience in the later use process, it is an essential prerequisite to strictly follow the specifications to implement every detail. This not only helps to improve the probability of success of the initial start, but also facilitates the smooth development of the follow-up maintenance work.
FAQ: Solving Your Doubts
for users often put forward on the frozen compressed air dryer problems were summarized, such as "why there will be frost blocking?", "how to judge whether the lack of freon" and so on. Through the specific analysis of these problems and the corresponding treatment measures, it is hoped that it can provide effective technical support information reference for the majority of users.
In the face of some sudden abnormal situations, having sufficient knowledge reserves can allow users to react more quickly and accurately, thereby minimizing the negative impact on production and life.
Future Trends
With the rapid progress of science and technology, the future of refrigerated compressed air dryers will develop in the direction of intelligence, integrating more sensor monitoring functions to monitor the trend of various parameters in real time. It is expected that the new generation models will also have higher energy efficiency and lower energy consumption characteristics, providing customers with a more environmentally friendly and economical product experience.
Keep pushing out
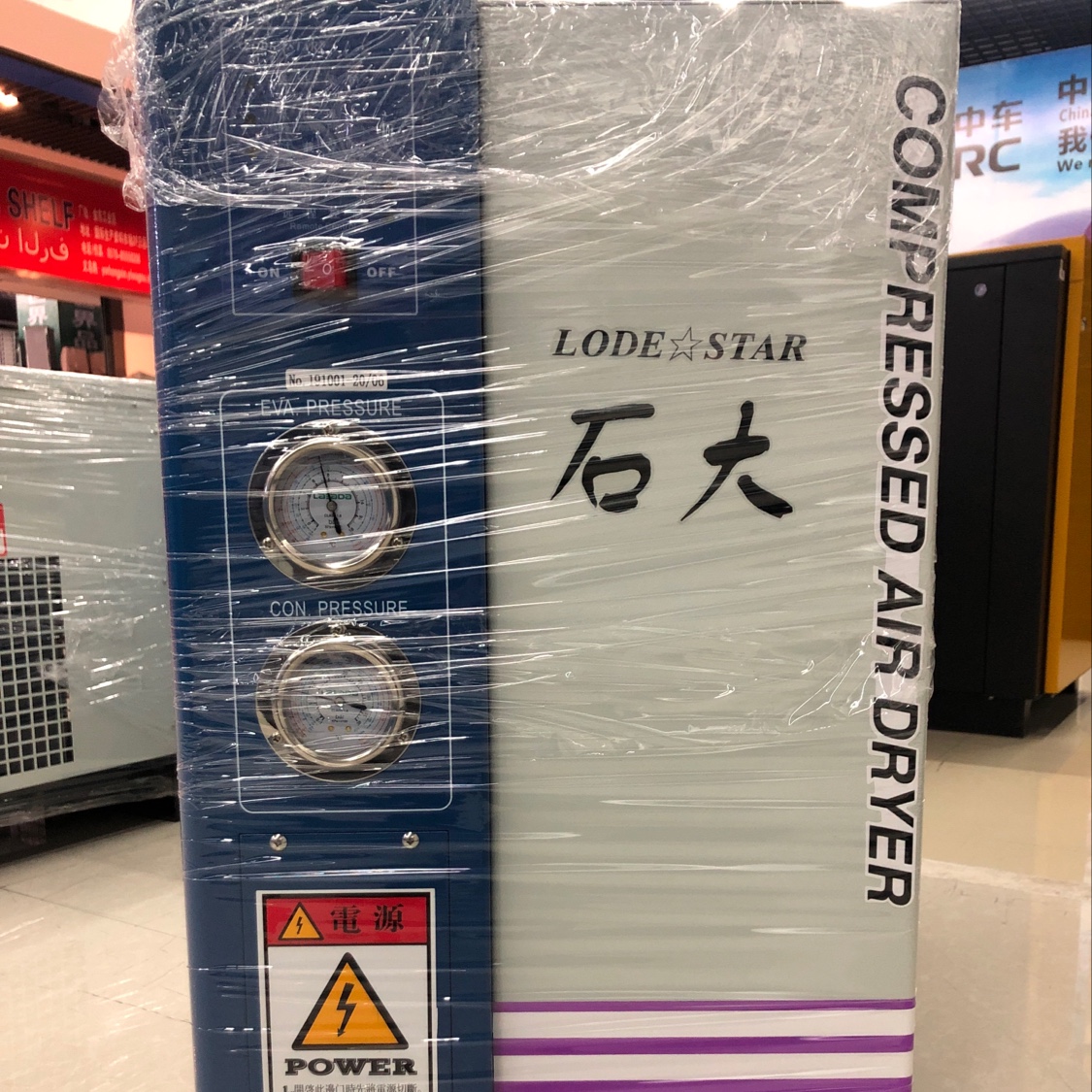