
Superior Quality-Built for Industrial Environments
Learn more about how this high-performance refrigerated compressed air dryer is specifically designed to cope with complex industrial environments. Highlight its rugged structure and ability to adapt to extreme temperatures and humidity, ensuring stable performance in any situation.
In the process of modern industrialization, the quality of compressed air directly affects the safety and efficiency of the production line. Therefore, an excellent compressed air dryer must be able to operate continuously and stably under variable and harsh working conditions. Our refrigerated compressed air dryers are constructed of high quality materials with excellent corrosion resistance and are equipped with advanced sealing technology to prevent dust and other impurities from invading internal components. Whether it is operating in cold areas or high temperature and high humidity environments, it can consistently provide pure and pollution-free compressed air resources.
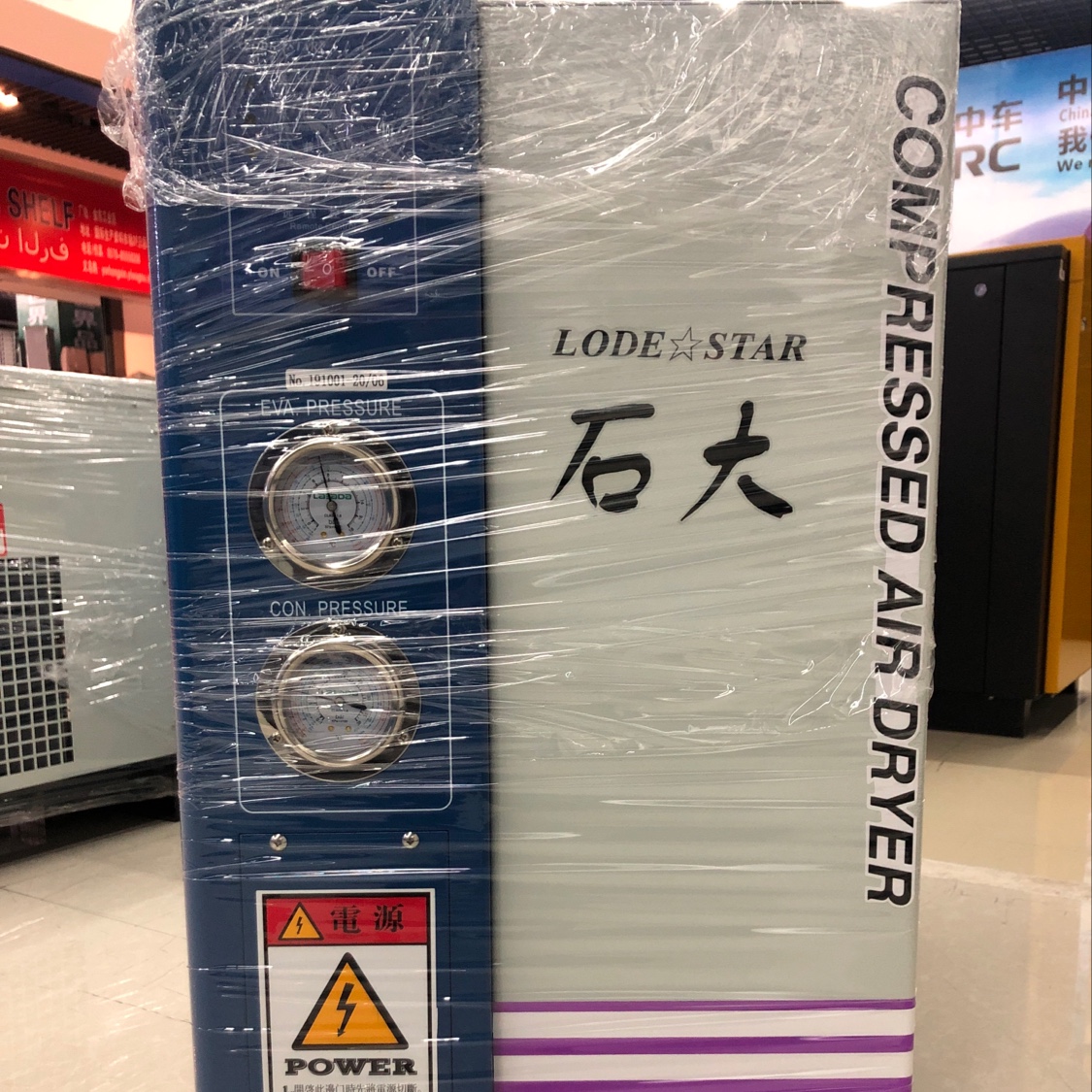
In-depth analysis-revealing the working principle
Explain the working mechanism of refrigerated compressed air dryers, including the refrigeration cycle process, the basic principles of condensation and dehumidification, and the functions of key components. Simplify complex concepts through illustrations or animations, making it easier for users to understand the technical mysteries.
When the compressed air containing water vapor enters the equipment, it first undergoes pre-cooling treatment, and then is sent to the evaporator for low-temperature exchange. At this time, the water carried in the air will quickly condense into liquid water droplets and be discharged out of the body, and finally obtain Dry and clean output gas. In order to ensure the efficient operation of the whole system, we have integrated a sophisticated control valve group and sensor network in the core part to monitor the parameter changes of each link in real time and adjust the operation mode in time to achieve the optimal energy consumption balance.
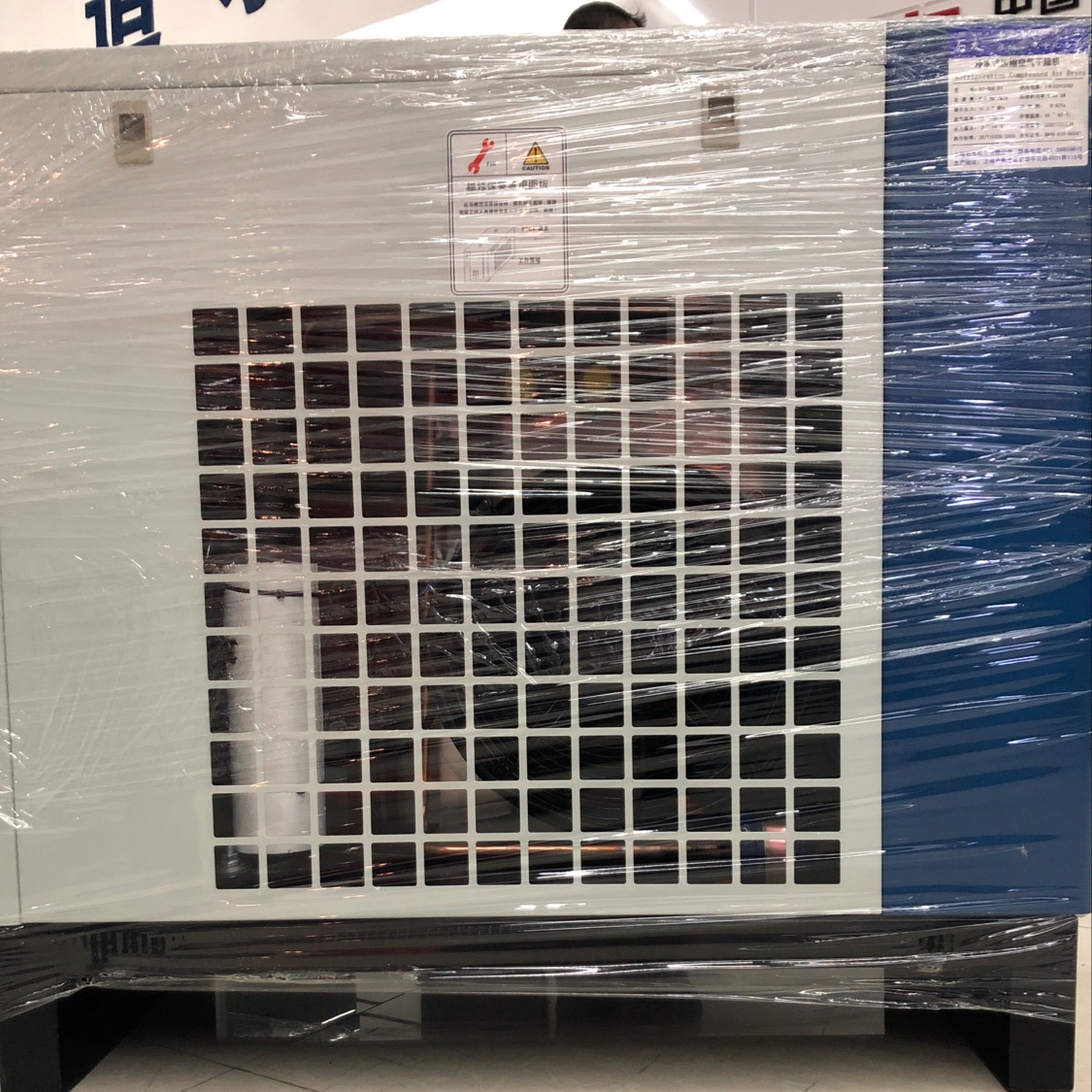
Core Technology-Efficient Purification
Focus on the core technology highlights of the equipment, such as efficient cooling system, intelligent control system and innovative filtration device. Analyze how these technologies work together to effectively remove moisture and other contaminants from compressed air and maintain low pressure loss.
We have adopted a unique dual-circuit refrigeration architecture, combined with large-capacity heat exchange plates, which greatly improves the cooling rate per unit time and shortens the overall processing cycle. At the same time, the built-in microprocessor is responsible for the overall management of all automated processes, covering detailed plans from power-on self-check to fault alarm. In addition, it is equipped with multiple filter element series mechanism, which is outstanding in intercepting oil mist particles, etc.
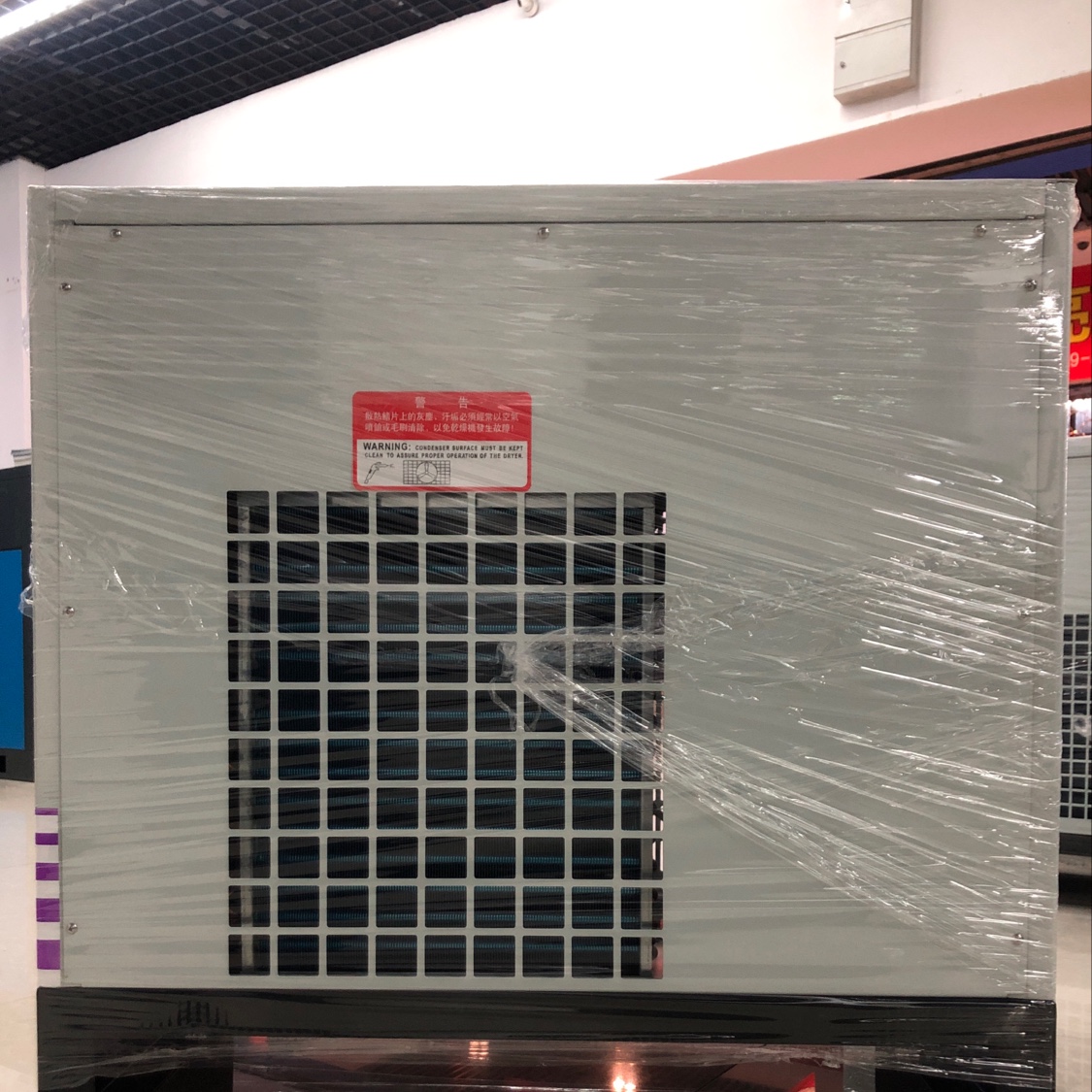
Widely applicable-meet diverse needs
A number of typical application scenarios are listed, covering manufacturing workshops, food processing industries, electronic semiconductor factories, and even scientific research laboratories. Professional purchase advice and installation guidelines are given for the specific characteristics of each type of place to ensure the best results and safety.
whether it is the dense pipeline network in large iron and steel smelters, the ultra-high purity raw material transmission line required in the preparation process of fine chemicals, or the pharmaceutical packaging assembly line with extremely strict health standards, the figure of this new dryer can be seen active. Customizing exclusive solutions according to the special requirements of different industries not only helps to improve work efficiency, but also brings significant cost savings to enterprises.
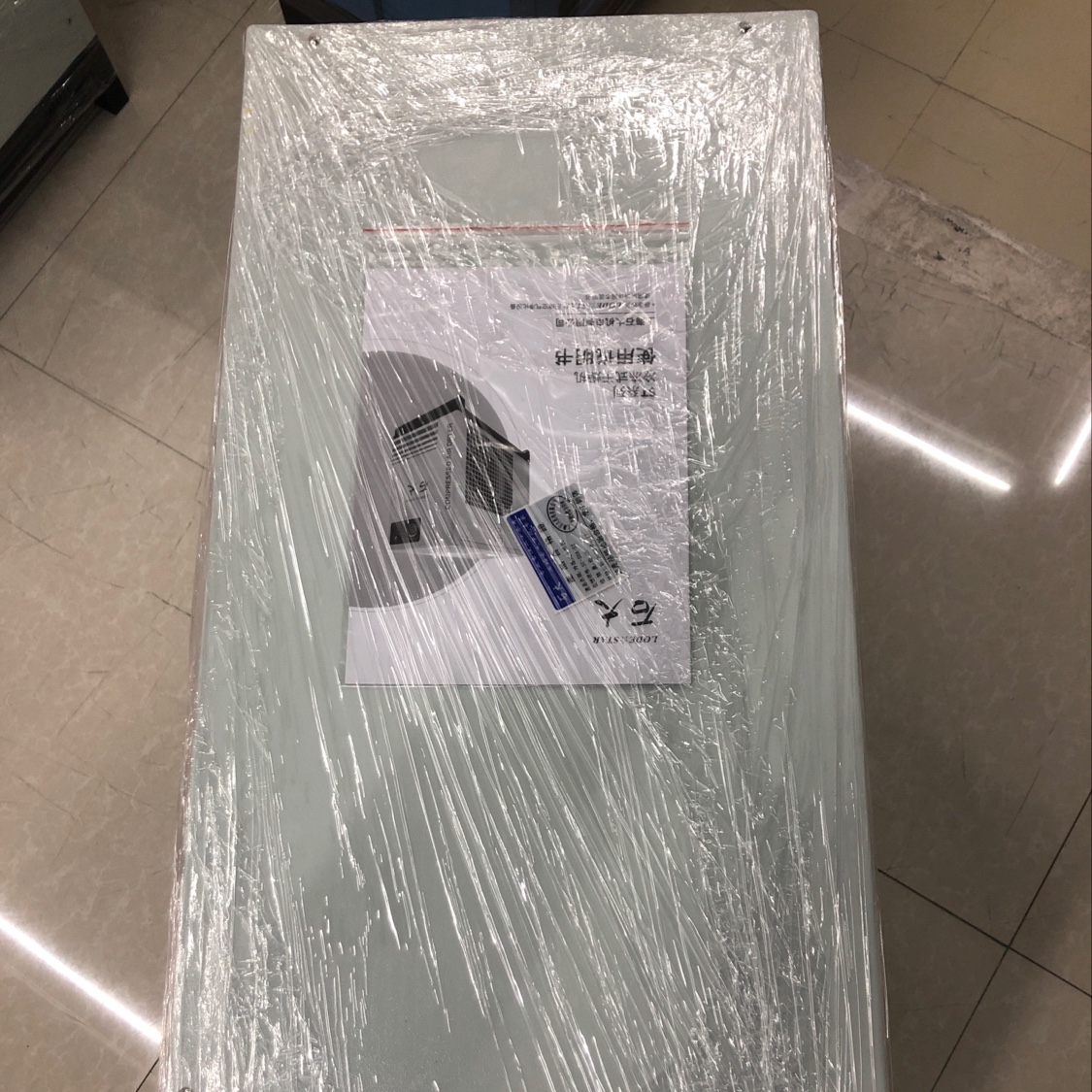
Affordable-Return on Investment Visible
Evaluate the economic benefits of using refrigerated compressed air dryers, not only in terms of initial acquisition costs, but also in terms of cost savings from reducing the number of breakdowns and repairs during long-term operation. The possibility of higher productivity due to improved air quality is also mentioned.
Although the initial investment may be relatively high, in the long run, choosing a high-quality refrigerated compressed air dryer is a very wise choice. On the one hand, it can greatly reduce the risk of production shutdown due to pipeline blockage or machine wear; on the other hand, clean compressed air is conducive to improving product quality, reducing the rate of defective products, and indirectly increasing the profit margin of the enterprise. According to actual case statistics, in some specific industries, such equipment can even recover all input costs and start to make profits in just a few years.
User Testimonial-Voice from the First Line
Bring together multiple customer reviews and case studies that have successfully deployed this product. Share their problems and solutions in practical applications, and show the good results achieved in the end. True stories are often more likely to touch the heartstrings of potential buyers and enhance their sense of trust in the brand's products.
A manager engaged in the production of auto parts said: "Since the introduction of this frozen compressed air drying system, we have found that the rust phenomenon in the workshop has been significantly reduced, which directly reduces the follow-up maintenance costs." Another engineer from a pharmaceutical company also mentioned: "Previously