
In the process of industrial production, compressed air is widely used as an important form of energy. However, when the compressed air contains too much moisture, it may cause a series of serious consequences such as pipeline corrosion, pneumatic tool failure, and product quality degradation. In response to these problems, refrigerated compressed air dryers have become the preferred solution for many companies.
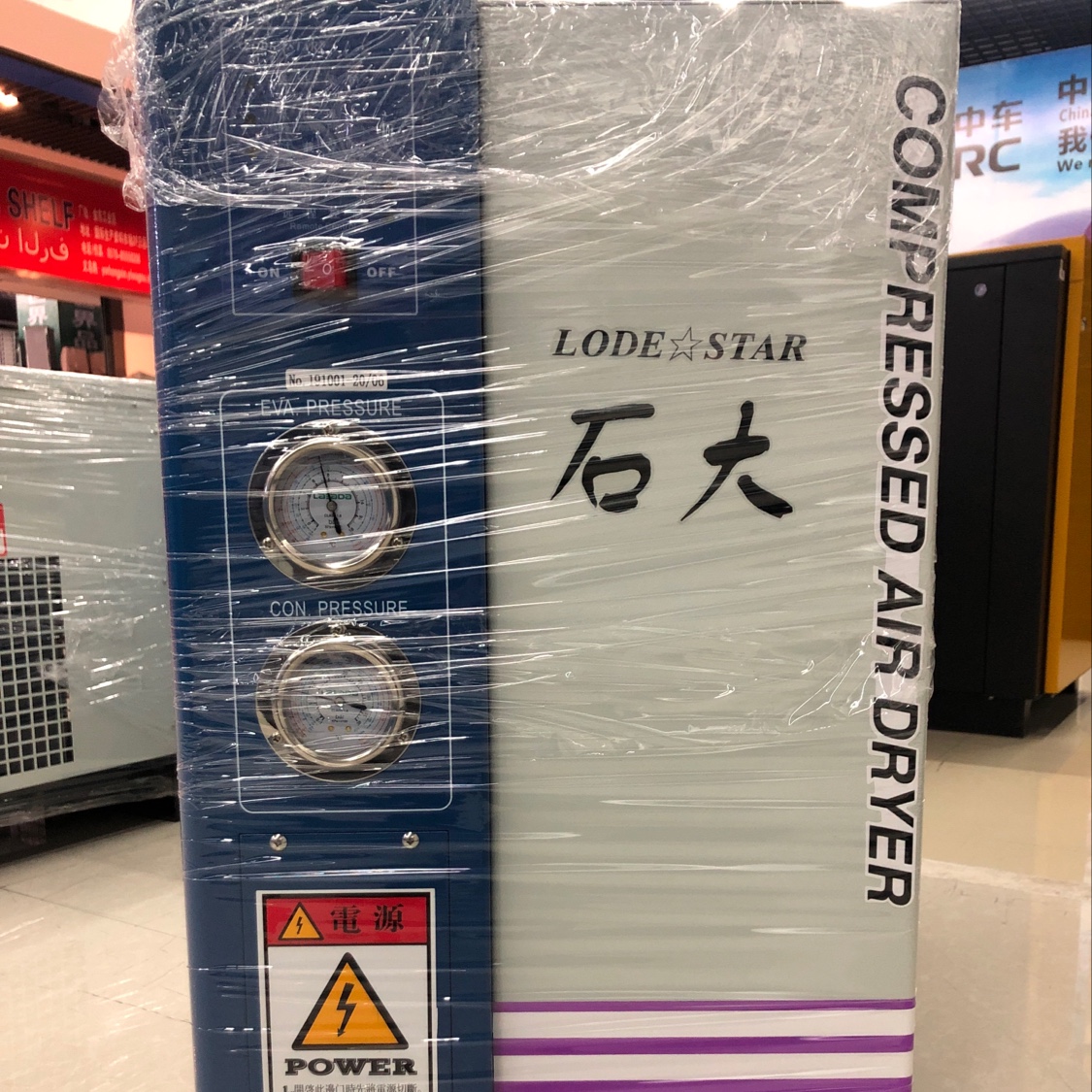
The core working principle of the refrigerated compressed air dryer is based on cooling and condensation technology. It reduces the temperature of the compressed air to promote the water vapor contained therein to reach a saturated state and condense into liquid water droplets, thereby achieving an effective dehumidification process. The equipment is equipped with evaporator and condenser components dedicated to heat exchange, ensuring high efficiency while maintaining low energy consumption levels.
At present, this type of dryer has been widely used in many industries. For example, in the field of food processing, sterile and clean compressed air quality is essential; and in the automotive industry, it is necessary to rely on a stable supply of low dew point value gas to complete precision process operations such as spraying operations. In addition, electronic component assembly lines or pharmaceutical factory workshops also rely on a compressed air environment with high high quality purity for daily operation and maintenance.
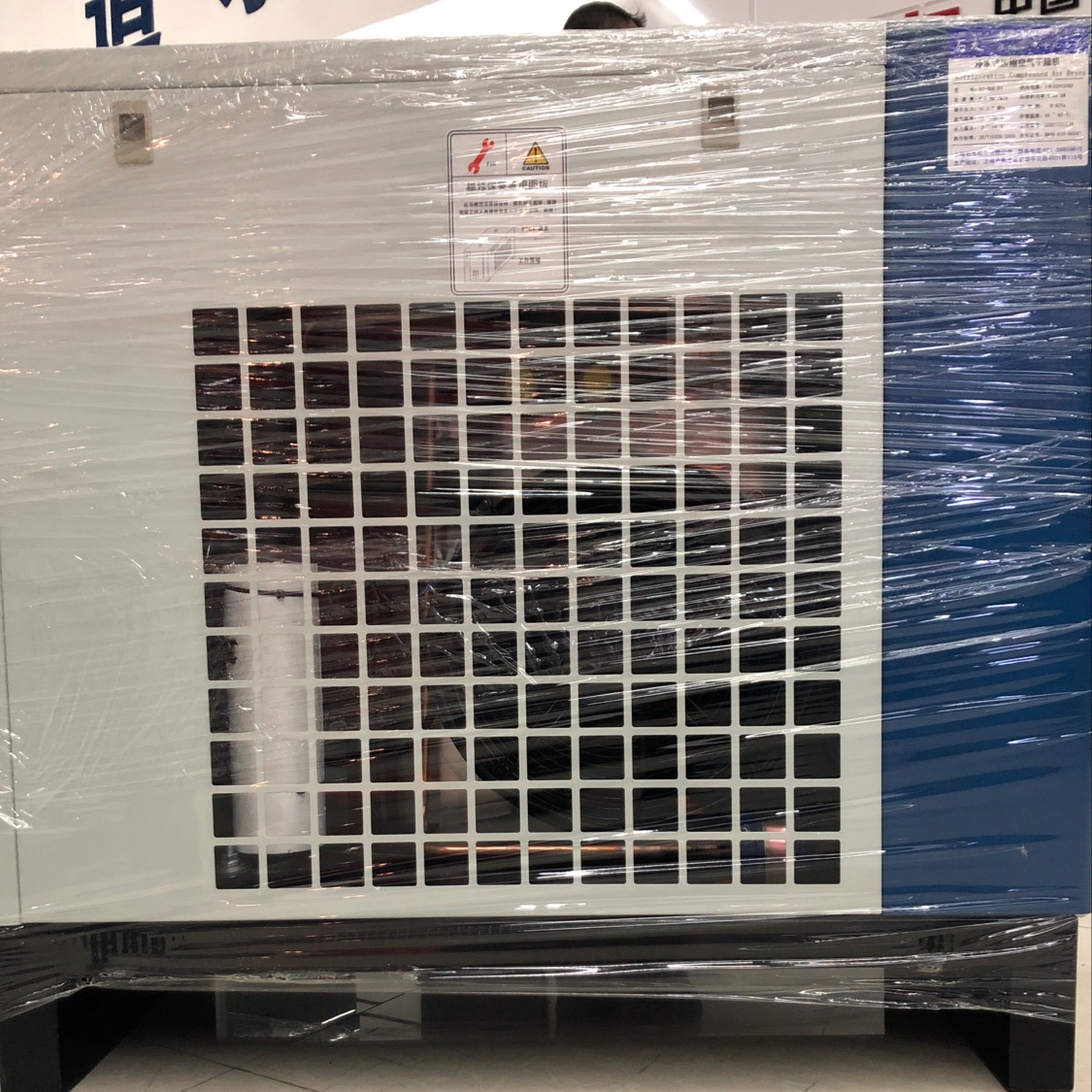
Compared to other types of compressed air processing units, refrigerated dryers have many distinct advantages. First of all, it is reflected in its strong reliability-due to the use of mature and stable mechanical refrigeration cycle system, it has a long life cycle and a very low failure rate suitable for long-term continuous operation mode of industrial field needs. Secondly, it is economical and practical, which is particularly worth emphasizing because compared with similar products, it can often save more operating costs, including less electricity consumption and low maintenance costs, which are all important factors for users to consider purchasing.
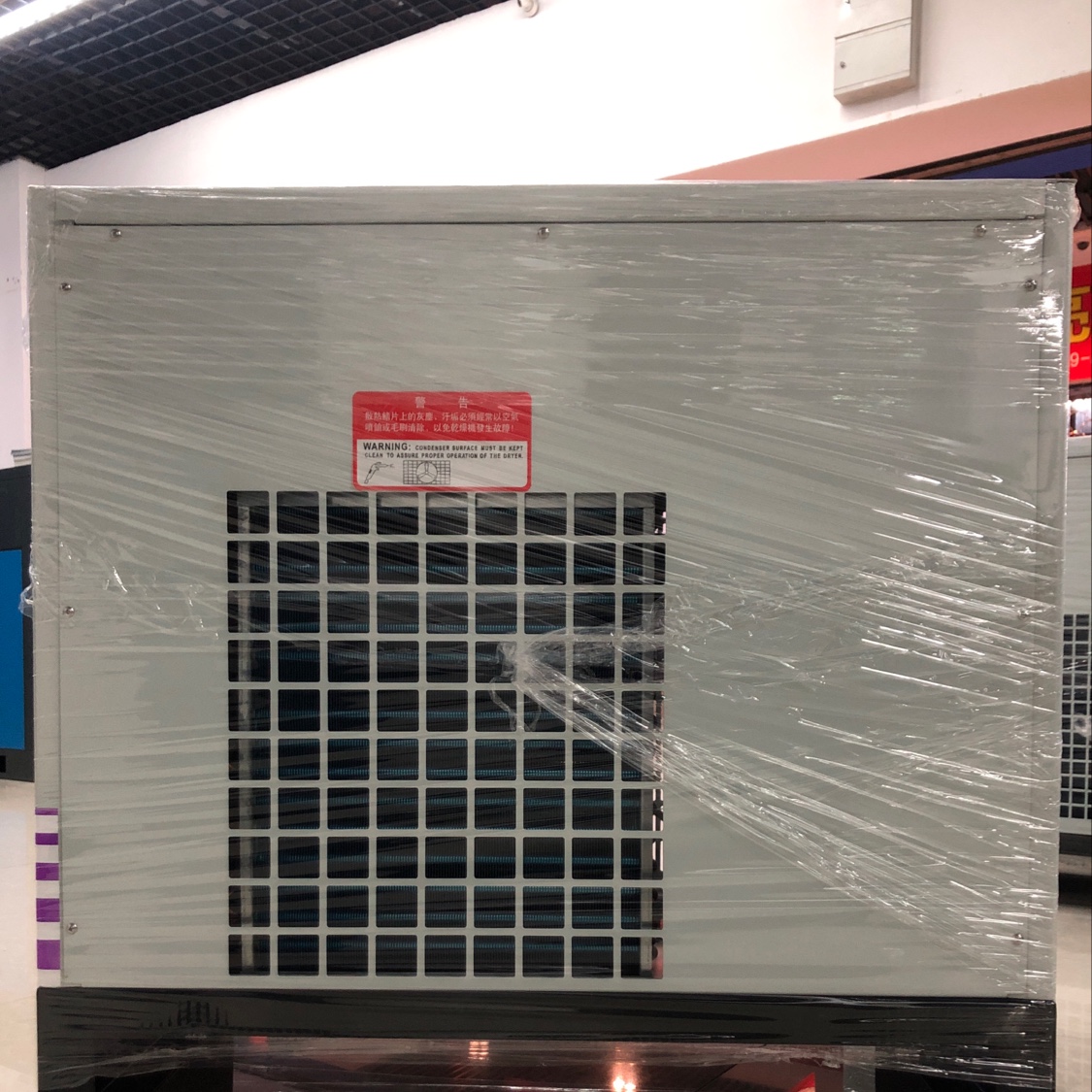
In view of the wide variety of choices on the market, how should we correctly select the refrigerated compressed air dryer suitable for the actual situation of our enterprise? The first task is to clarify its own specific parameter requirements, such as the maximum flow range value, import pressure limit conditions and other factors, and then screen out the model specifications that meet the conditions, and then comprehensively evaluate the brand reputation, after-sales service guarantee measures and other information to make a wise decision.
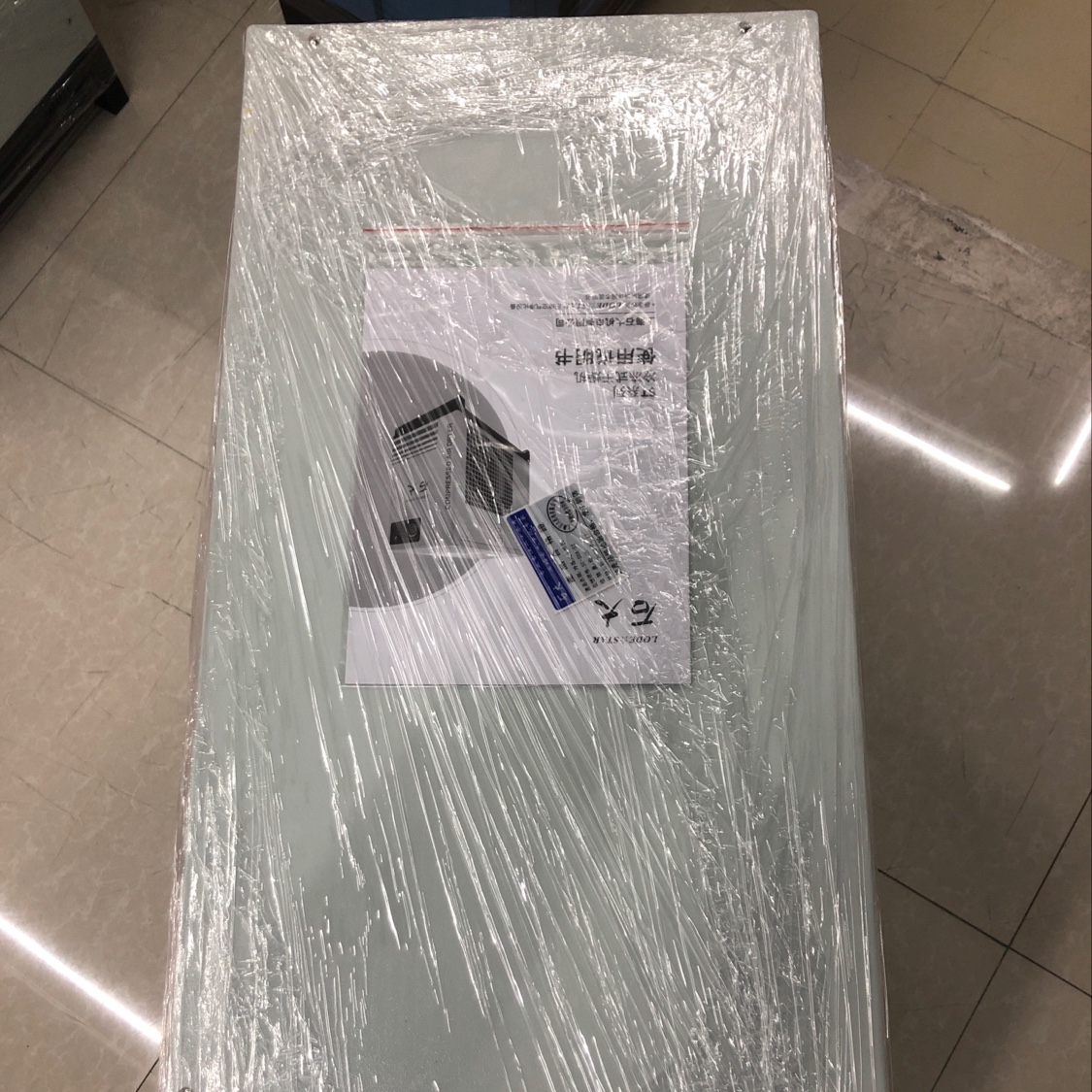
In summary, choosing a high-quality refrigerated compressed air dryer can not only help companies significantly improve various potential risks caused by humidity, but also further optimize the overall production process and create greater economic value.
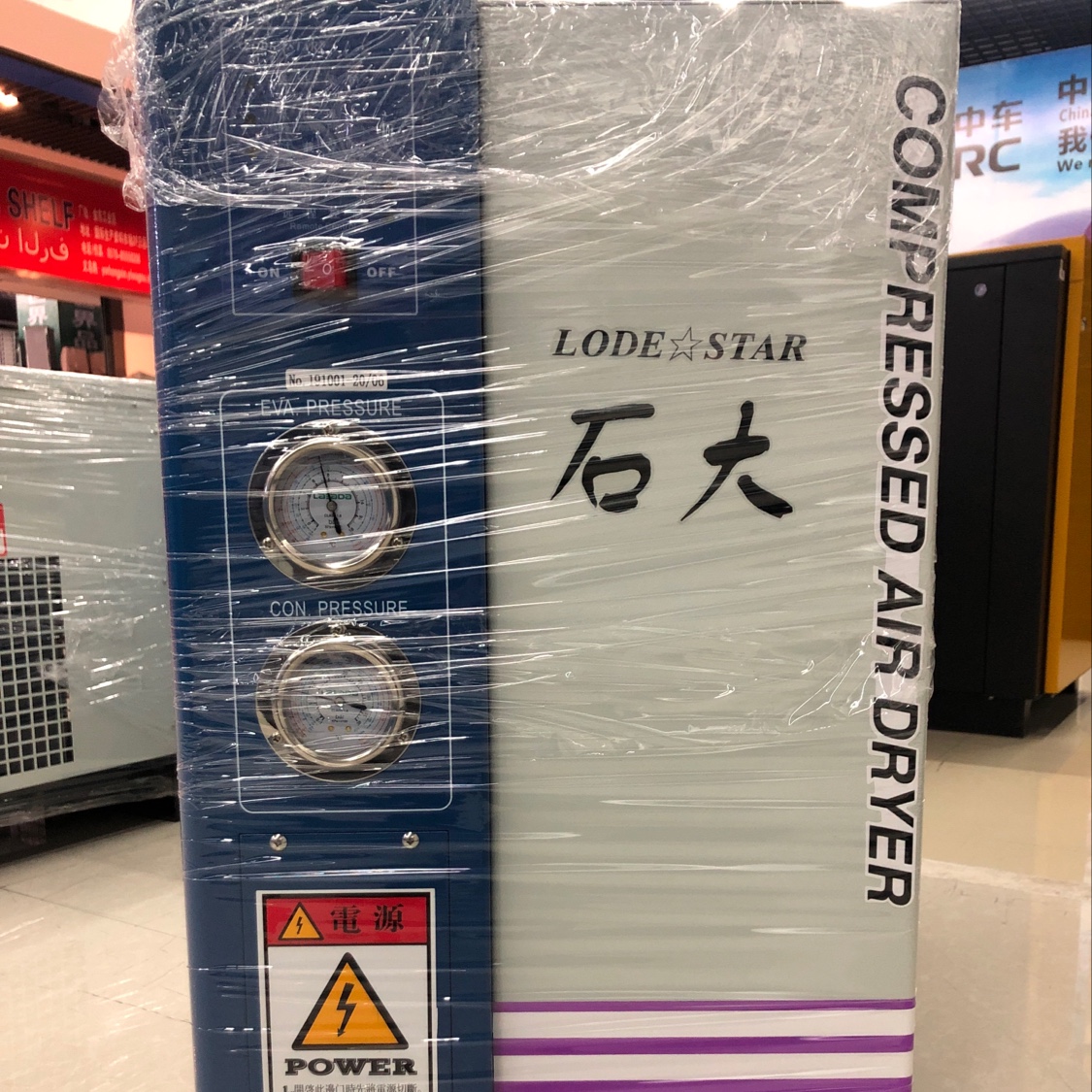